Stamping and deep drawing is an industrial metal transformation technique combining precision and efficiency. This process is highly valued in demanding sectors such as automotive, home appliances, and construction. While it may seem complex, this method becomes accessible with clear explanations and practical advice. This comprehensive guide is specially designed for beginners, detailing the steps, tools, and tips needed to get started in stamping and deep drawing.
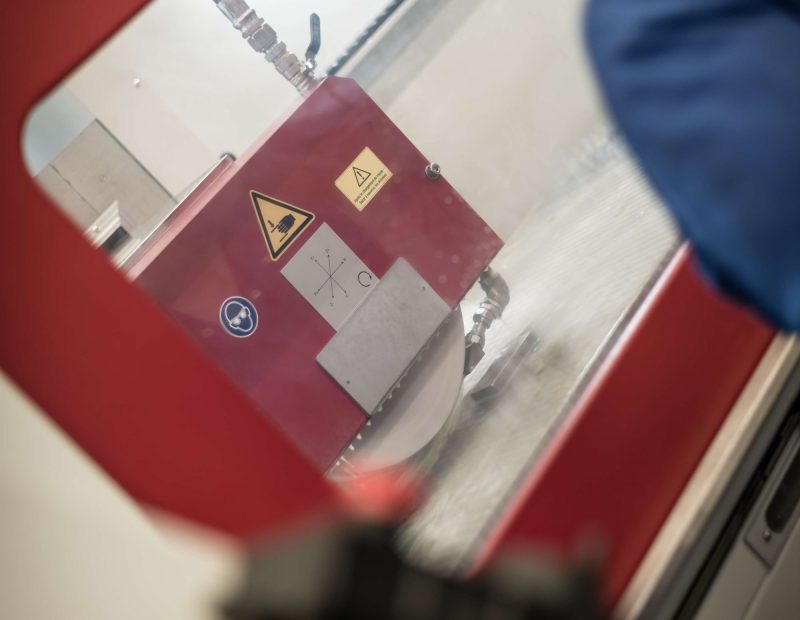
What is Stamping and Deep Drawing?
Stamping and deep drawing combine two distinct processes: cutting and forming. These two techniques transform flat sheets into structured and functional metal components. Cutting involves separating a portion of material according to a predefined shape, while forming deforms the material to achieve a three-dimensional volume. This process is essential for producing complex parts in large series, thanks to its ability to deliver precise and repeatable shapes.
Unlike additive manufacturing methods, which build parts layer by layer, stamping and deep drawing directly reshape a metal sheet. This technique is prized for its ability to produce uniform and reliable parts, essential in industries such as automotive, where each component must meet strict quality criteria.
The Advantages of Stamping and Deep Drawing
- Precision and Uniformity: The ability to reproduce identical parts with minimal tolerance makes stamping and deep drawing a preferred technique for sectors requiring strict quality control.
- Production Speed: Automated press lines allow for high-volume production with a quick production cycle. At Ouréval, presses ranging from 25 to 400 tons ensure sustained throughput while maintaining quality.
- Material Flexibility: Steel, aluminum, stainless steel… Each material can be transformed through stamping and deep drawing, offering significant adaptability depending on project needs.
- Economies of Scale: By producing parts in large quantities, companies can optimize costs and achieve significant savings.
To explore concrete examples of these advantages, check out the stamping and deep drawing solutions offered by Ouréval.
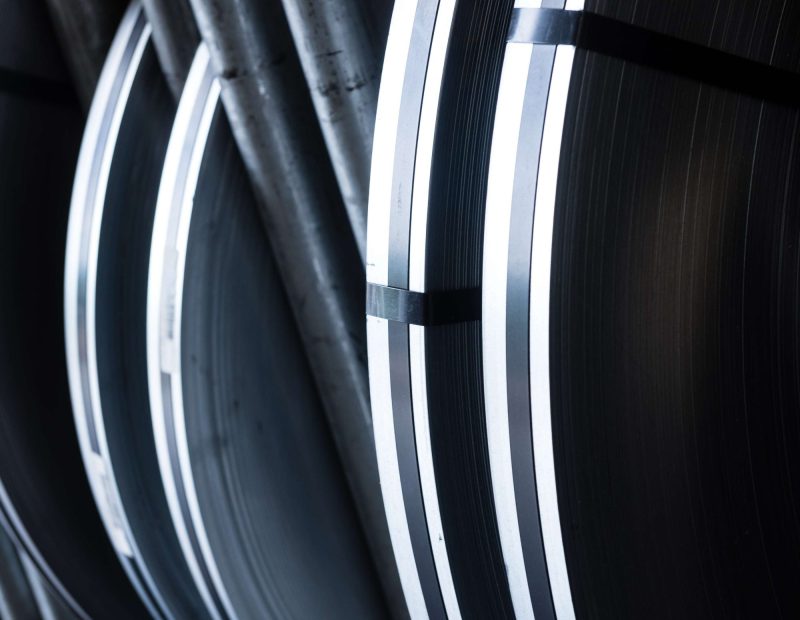
Commonly Used Materials
The choice of material is crucial as it directly impacts the quality and durability of the produced parts. Depending on the final application, various metals can be selected:
- Steel: This material is widely used for parts requiring high strength. It is commonly found in sectors such as automotive for structural reinforcements.
- Aluminum: Lightweight and corrosion-resistant, aluminum is preferred for parts exposed to the elements or when reducing the final product’s weight is a priority.
- Stainless Steel: For sectors where corrosion resistance and aesthetics are key, stainless steel is often the best choice.
Essential Tools for Stamping and Deep Drawing
The quality of stamping and deep drawing depends on the equipment used, particularly presses. At Ouréval, these machines are operated with computer numerical control, ensuring increased precision. The quality of the tool also plays a vital role. A poorly designed tool can result in defects, underscoring the importance of meticulous design. Regular maintenance is necessary to ensure clean and precise cuts, extending tool life and reducing defect risks.
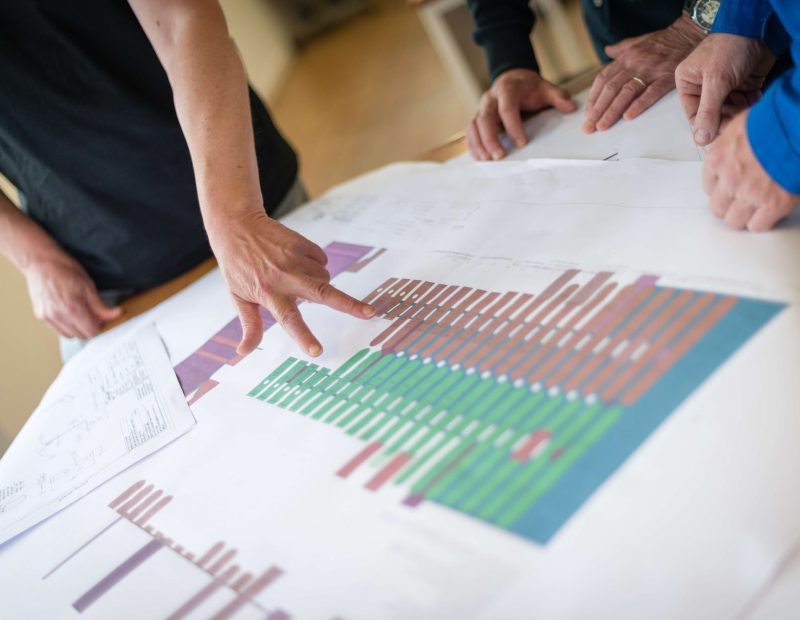
Steps in the Stamping and Deep Drawing Process
Needs Analysis and Design
The first step involves thoroughly analyzing the client’s specifications and project requirements. Designers use CAD (Computer-Aided Design) software to model the specific press tool. This allows simulation of the sheet’s behavior under pressure and identification of potential issues before the manufacturing phase.
Prototyping and Pre-Series
Once the tool is designed, prototypes or pre-series are produced. These samples are essential for testing feasibility and adjusting production parameters such as pressure or stroke speed. At Ouréval, initial parts are produced on presses up to 400 tons, ensuring samples representative of the final series.
Prototyping is particularly crucial for detecting potential defects and ensuring the final part meets all technical specifications.
Start of Mass Production
After prototype validation, mass production begins. The metal, often in coils, is unrolled and cut to the required dimensions, then formed into the final shape. At coils up to 660 mm wide, with sheet thicknesses ranging from 0.5 to 6 mm, offering great flexibility for industrial applications.
Quality Control
Quality control is an essential step to ensure that each part meets the required tolerances and specifications. Ouréval implements frequent quality control procedures throughout the process to guarantee the conformity of produced parts. This quality approach is reinforced by ISO 9001 and IATF 16949 certifications, ensuring reliable production that complies with international standards.
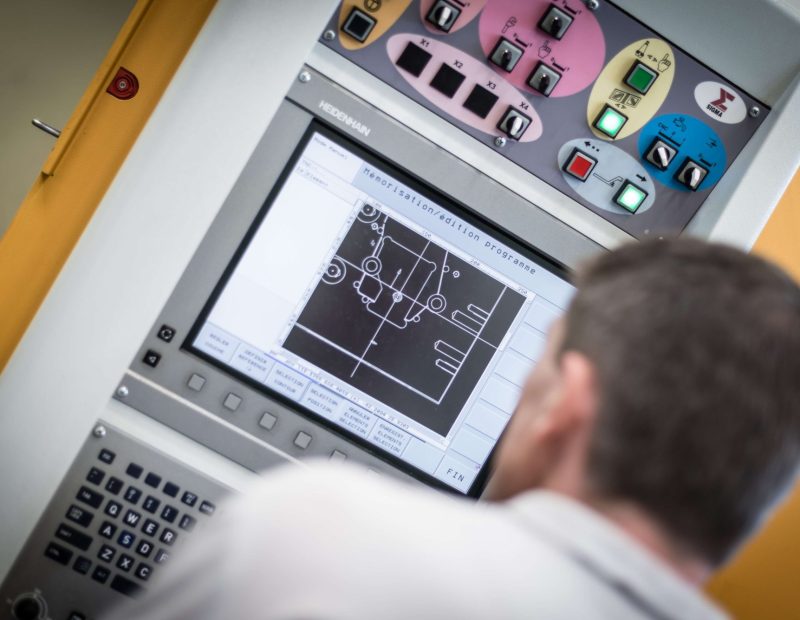
Practical Tips for Beginners
Choosing the Right Material
Material choice is crucial for the final quality. Hard steel may be suitable for structural parts, but for products requiring lightness and corrosion resistance, aluminum is preferable. Each metal has unique deformation and resistance characteristics that are essential to understand for a successful project.
Mastering CAD Tools
CAD tools allow for visualizing parts and simulating their behavior before production. This step reduces errors and enhances precision from the design stage. Beginners are advised to learn the basics of CAD, which facilitates collaboration with the design team and provides a better understanding of the technical constraints of each project.
Following Quality Control Procedures
Rigorous quality control at every step maintains the precision and quality of produced parts. Methods include dimensional checks and tolerance controls, essential for avoiding defects in series production.
Encouraging Collaboration
Stamping and deep drawing often involve multiple teams (design office, press operators, quality control) working together to achieve optimal results. Communication and collaboration are crucial to avoid errors and ensure smooth production processes.
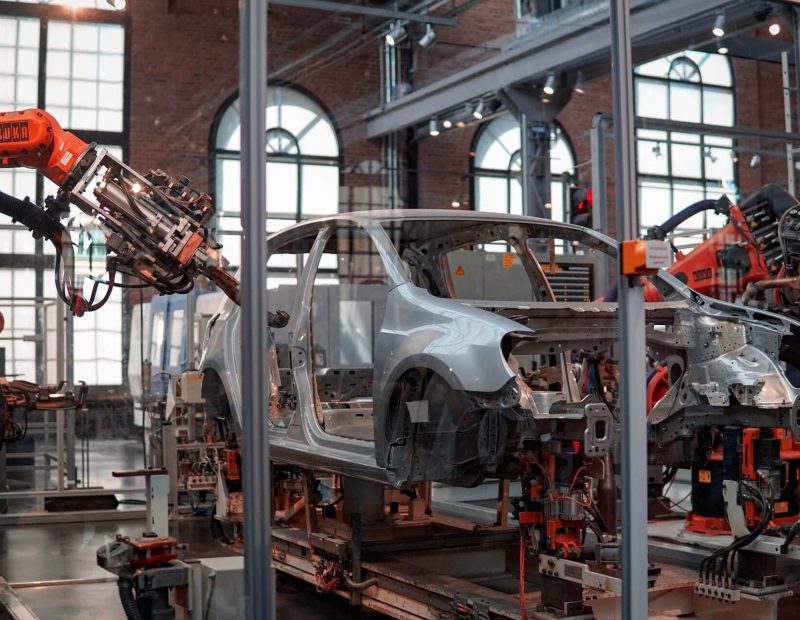
Industrial Applications of Stamping and Deep Drawing
Stamping and deep drawing have extensive and varied applications:
- Automotive: This sector extensively uses this method for structural vehicle elements, such as body reinforcements and air conditioning components. Due to strict quality requirements, Ouréval has become a trusted partner for automotive suppliers.
- Home Appliances: Stamping and deep drawing are essential for internal components of home appliances, such as supports and deflectors in ovens. The durability of produced parts ensures reliability in high-temperature environments.
- Energy and Construction: This method is used for components like protective enclosures for ventilation systems and structural supports. These parts require increased robustness to withstand demanding environments.
- Office Furniture and Packaging: In furniture, this technique produces metal desk legs and structural reinforcements. It is also used for industrial packaging, particularly for shock- and deformation-resistant containers.
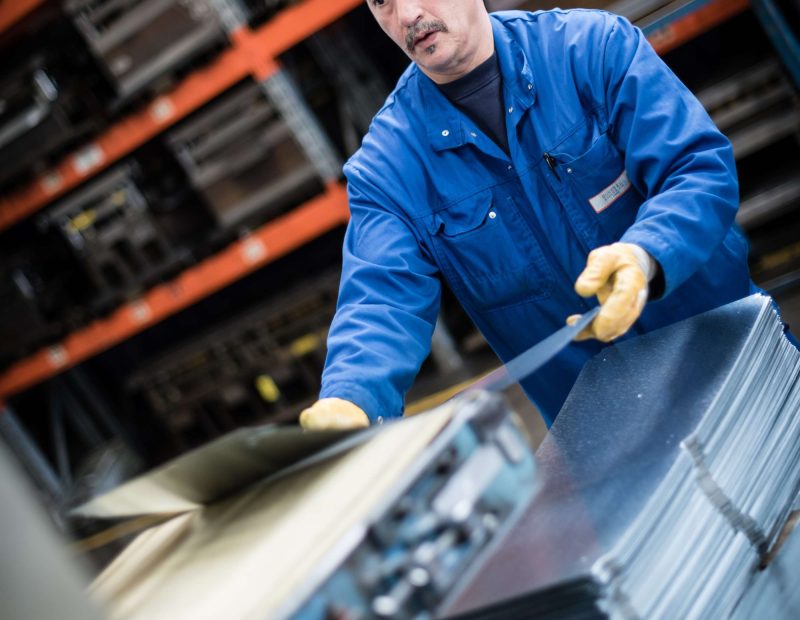
Advanced Tips for Optimizing Stamping and Deep Drawing
Investing in Quality Tools
Robust and well-maintained press tools reduce long-term costs by minimizing waste and defects. Regular tool maintenance extends their lifespan and ensures optimal cutting quality.
Automating Quality Control
In large-scale production, automating quality control ensures consistency and reduces human error. Industrial vision systems can verify dimensions and tolerances in real time, guaranteeing conforming production.
Selecting Materials Strategically
Material selection should be optimized for each project based on its final application. For example, for parts used in corrosive environments, stainless steel or treated aluminum is more suitable, avoiding costly surface treatments.
Working in Co-Development
Co-developing with suppliers and clients from the design phase is an effective way to optimize the final product while reducing manufacturing costs. This collaborative approach addresses technical constraints early, avoiding costly adjustments during production.
Ultimately, stamping and deep drawing is more than just a metal transformation technique; it is a sophisticated industrial process capable of producing precise, reliable parts tailored to the demands of large-scale production. By combining technical expertise, state-of-the-art equipment, and rigorous quality control methods, companies like Ouréval position themselves as trusted partners for numerous industrial sectors, from automotive to construction.
For beginners, familiarizing themselves with the steps and tools of this method is essential to understanding its potential and constraints. With time and experience, mastering this technique opens up many possibilities for customization and optimization, making stamping and deep drawing an indispensable asset for any serial production project.
To learn more, explore the stamping and deep drawing solutions offered by Ouréval.
A certified quality partner
for the overall management of your projects
Comprehensive solution
From the prototype to the delivery of series parts to the client
Tailored production
Medium and large series
50 years of experience
30 people at your service - recognised know-how and expertise
Certified quality
Certification according to ISO 9001 and IATF 16949